It seems perplexing that in a region famed for its trees, a walk through any area lumber yard feels like an impromptu trip around the world.
Dimensional lumber — the 2-by-4 and 2-by-6-inch wooden planks that are synonymous with conventional construction — routinely comes from far-away places such as the Czech Republic or Chile, while trees felled in local backyards end up as firewood or mulch and the odd piece turned into a rustic bowl or whittled into an old-timey toy.
But a handful of local construction professionals participated in a timber-framing workshop last week, hoping to create a renewed interest in a somewhat forgotten building practice and scale up the use of locally grown trees. Their goal over four days — under the supervision of a Vermont-based team of instructors — was to frame and raise a barn from heavy timber cut from a stand of white pine, then milled on-site at Morningside Farms in Brevard.
Timber framing, also known as post-and-beam construction, refers to a building method that eschews metal fasteners and dimensional lumber and instead creates structures with carefully fitted and joined heavy, squared-off timbers, milled from local trees.
It’s that latter aspect of timber framing that workshop lead instructor Matthew Agrella-Sevilla hopes will help him find a nurturing environment for his professional passion in Western North Carolina.
“We are surrounded by the most amazing resource right here. We have trees — really big trees, here,” says the 40-year-old Vermont resident, who is in the process of relocating to WNC this summer, along with his wife and 2-year-old son.
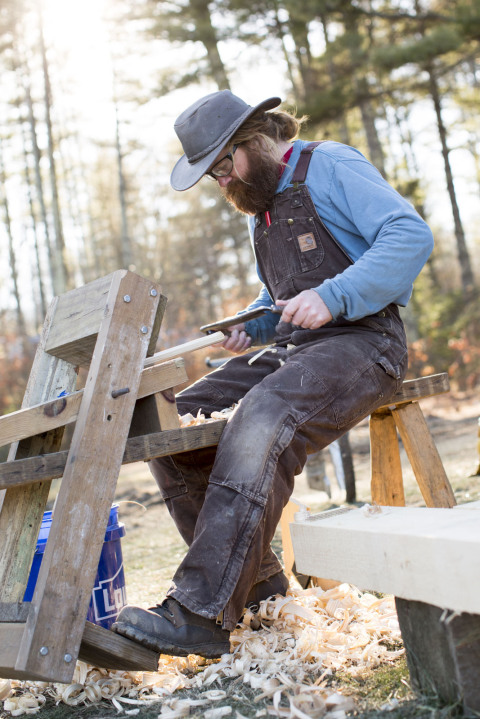
“It makes great sense when someone has a lot of timber on their building site and likes to do things locally,” says Kris Forward, 35, a second-generation carpenter and contractor who co-owns Forward Construction in Asheville with his parents.
Forward, who thinks there is a local demand — though not necessarily a big one — for timber-framed projects, says he signed up for the $350 workshop to expand his professional horizon, a sentiment echoed by most of the other workshop participants. “I’ve always been interested in learning it,” he says, eyes twinkling behind safety glasses. “It’s so eclectic and just so different from what we normally do.”
“It’s a trade. It’s a skill set to add,” says Mark Wulff, a 33-year-old Asheville builder, who, along with his business partner Josh Brown, 32, both of Brown Wulff Home Services, signed up to gain an early foothold in what they believe could become a back-to-the-basics trend in the local building world, akin to the farm-to-table movement in the area’s dining scene.
“With traditional construction, there is a lot of ways to pick it up,” says Wulff. “Learning this in this kind of setting is a special opportunity,” he adds, pointing to the scattering of Carhartt -clad men hunched over a dozen heavy beams or perched on saw horses in a sunny field. With a mix of old-tradition hand tools and compressor-powered power tools, they are learning to make intricate joints that will require little beyond arm-long wooden pegs to hold the 24-by-40-foot structure that will house two horses.
The tone is jovial and relaxed. Several builders remark how much they enjoy not being in charge and having their work checked by the steady hands and discerning eyes of the Vermont instructors before each final cut. The idyllic farm, owned by John and Cherie Felty, is home to one of Brevard first CSAs and has at times operated as a bed-and-breakfast.
But idyllic setting and casual camaraderie aside, there is little room for mistakes in this type of building. “It’s so three-dimensional,” says local builder Chris Faulkner of Faulkner Woodworking. He’ll help finish the project once the workshop is over. “Traditional construction is two dimensional — up and out — but this tickles a different area of the brain.”
Great article about a time-tested craft.