In early 2021, Graham Sharp, guitarist and banjo player for the local Grammy Award-winning bluegrass band Steep Canyon Rangers, was preparing to release his solo album, Truer Picture. But problems soon emerged. Due to supply chain snags brought on by COVID-19, his label, Yep Roc Records, couldn’t get vinyl copies made by its usual European producer.
Thinking fast, Sharp turned his attention to Citizen Vinyl, North Carolina’s first vinyl record pressing plant, which launched in downtown Asheville in October 2020. After Sharp visited the venue, his label agreed to work with the local company.
Fast-forward to today, and Sharp says he was so impressed by Citizen Vinyl’s quality that Steep Canyon Rangers are preparing to press their next album, Morning Shift, with the local company as well.
“Everybody’s superexcited about the prospect of pressing our music right here in Western North Carolina,” Sharp tells Xpress.
For musicians and fans alike, Citizen Vinyl is one of two local options within the unique industry. Shortly after its launch, the company was joined by American Vinyl Co., located on the South Slope. Both shops opened amid an upswing within the trade. According to Billboard, the vinyl industry saw a 46.2% year-over-year increase in sales in 2020; in 2021, total sales continued to climb, increasing by an additional 5%.
But the wave has shown signs of slowing. In 2022, for example, sales rose only 4.2%. Meanwhile, local producers say a more pressing issue is the reliance on a diminishing number of machine parts and materials suppliers, as well as experts who can service and repair these devices.
“With this industry, it is usually just one supplier at every stop,” says Ryan Schilling, American Vinyl Co.’s owner and founder. “All across the industry, whether you’re pressing or cutting records, we all feel that kind of strain once in a while, and we wake up in the middle of our sleep hoping we have our materials the next day.”
But it’s not all doom and gloom. Shared struggles within the industry, says Schilling, have fostered a spirit of collaboration. Locally, the two record-making companies have recently started working together, with American Vinyl Co. manufacturing the lacquer master discs that Citizen Vinyl uses to press its vinyl copies.
“We have a very cohesive, complementing business,” Schilling says.
Quality over quantity
Citizen Vinyl’s production manager, Seth Alder, the company’s first hired employee, began as a technician. Today, he oversees all steps related to production — from ordering materials to sending files out for cutting and plating.
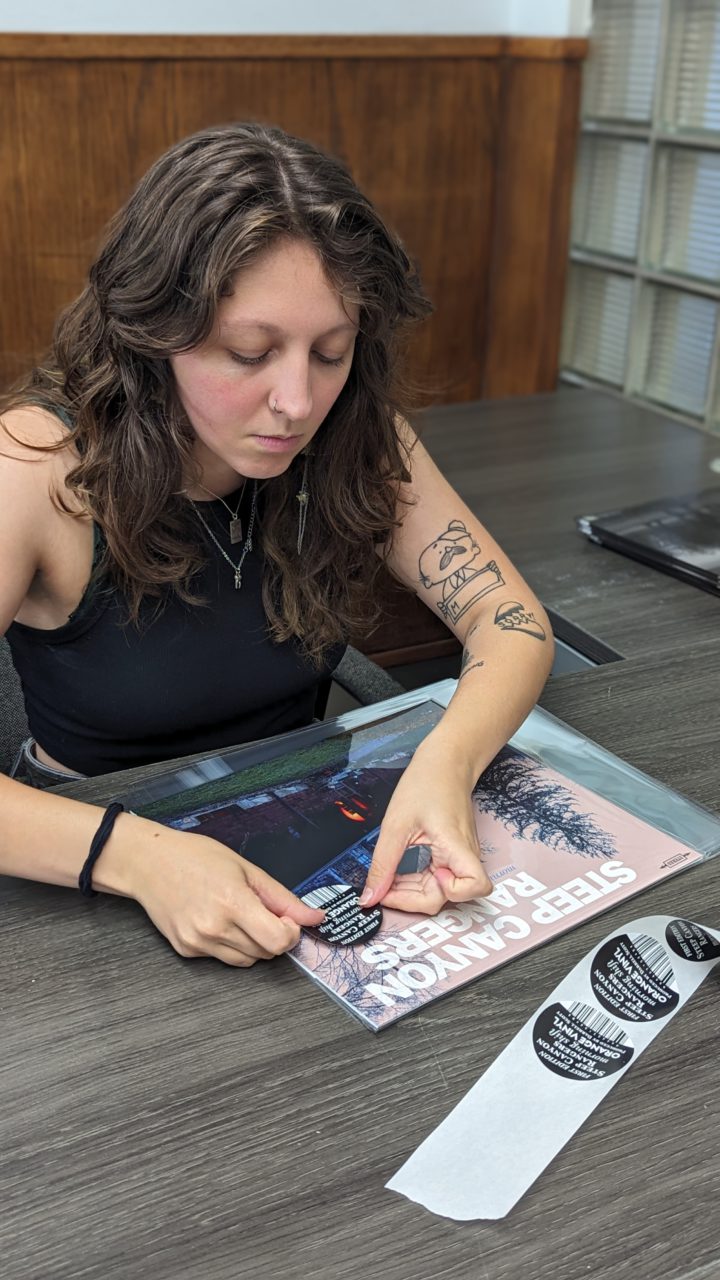
Despite Citizen Vinyl opening during COVID, he says the company weathered the pandemic relatively well. The PVC pellets used to make vinyl records never ran short, though cardboard and paper product shortages made producing the sleeves, jackets and center labels challenging. More concerning was a significant rise in ocean freight costs.
“Now they’ve come back to reasonable levels,” Alder says. As a result, he continues, Citizen Vinyl released a new, lower price list on June 1.
To make its records, the plant uses three pressing machines, including a new semiautomatic press made in Canada and an automatic machine custom built by Record Pressing Machines in Pegram, Tenn. The same company also updated Citizen Vinyl’s “workhorse” press, an automatic SMT 1500 originally produced in the late 1970s.
“As far as parts go, we do have one or two suppliers,” Alder says.
But if those suppliers have a backlog of orders, he continues, the staff has to improvise. “It is definitely hard to find good personnel for this industry,” he notes.
Nevertheless, the plant has developed an impressive client list in just a few years. “We get a lot of North Carolina artists or North Carolina labels that press their artists with us,” Alder explains. Among those are local musicians Angel Olson and Moses Sumney, as well as the Piedmont-based bluegrass group Chatham Rabbits and electronic duo Sylvan Esso out of Durham.
Farther afield, Citizen Vinyl handled the reissue for acclaimed New York hip-hop artist MF Doom after his death in 2020; at 24,000 records, it was the company’s largest order to date. Other famous clients include LCD Soundsystem, Wu Tang Clan, Depeche Mode and Mobb Deep.
With the pandemic vinyl boom, the company was quickly swamped with orders. Alder says the firm only caught up with its backlog at the end of 2022. Now, the focus is on winning over new clients with innovative designs and technology. The company offers records in solid colors, as well as colorful splatter and marble swirl patterns — both of which, Alder notes, are increasingly popular with buyers, especially collectors.
The company also created a vinyl NFT, or nonfungible token. A radio frequency identification chip is embedded in the record that stores transaction data. If the record is ever sold, a percentage of the resale value will go back to the original artist.
Most of all, Alder says, Citizen Vinyl emphasizes painstaking quality control at every stage of production. Larger presses focused on quantity might only inspect one out of every 100 records, he notes. But at Citizen Vinyl every record is inspected multiple times.
“They’re all visually checked by hand,” Alder explains. “We’ve built a reputation for our quality.”
Reviving a dying art
Down on South Slope, Schilling notes he became obsessed with record cutting in the mid-2010s. At the time, his options for learning the process were limited. He ended up traveling from his home in California to southwest Germany to apprentice with a master who had set up his lathe in a barn.
“I trained for basically like 48 hours straight, with very little sleep,” Schilling remembers.
Soon after founding American Vinyl Co. in 2016, he and his partner, Christy Lynn, moved to Asheville, having fallen in love with the city when they toured here with their musical act, the Christy Lynn Band.
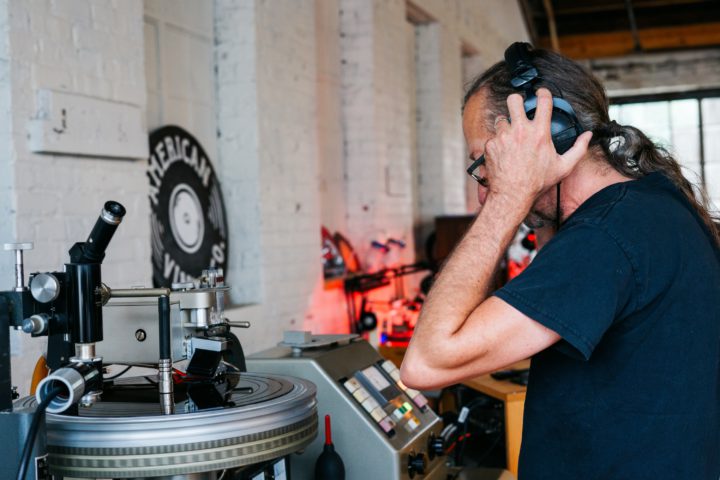
Of the seven manual lathes American Vinyl Co. has in its Coxe Avenue shop, the ones used for short runs of up to 30 copies can easily fit on a desktop. For the larger runs, employees rely on a 1966 Neumann lathe that Schilling calls their “workhorse.”
This lathe is used to cut lacquer master discs for vinyl pressing plants. The quality of these masters is superior to vinyl records, but they are also incredibly fragile. “After about 10 plays, you would start losing all your high end on the audio because it’s literally like a soft wax,” Schilling explains.
Lacquer is also incredibly flammable, a quality that devastated the industry when the Apollo Masters factory in Banning, Calif., burned down on Feb. 6, 2020. According to Rolling Stone, the factory was responsible for approximately 70%-80% of all lacquer discs worldwide. Now, only one factory in Tokyo remains.
According to Schilling’s estimates, there are roughly 30 professional cutters in the country. With such low numbers, the greatest concern is ensuring that the knowledge of this craft continues.
“We all have this group mentality of keeping the knowledge distributed between us and stored away for safekeeping,” he says. “Each one of us holds a part of it.”
Like Citizen Vinyl, American Vinyl Co. blends older technology and history with modern sensibilities. The company also puts out splatter and color records, as well as records in a variety of shapes like hearts and stars.
With its mobile recording studio the American Sound Truck, Schilling and his staff of five can also cut records live, carrying on the tradition of recording pioneers such as ethnomusicologist Alan Lomax. Among the company’s many features, it has a live recording booth in the shop where customers can walk in, record a song and leave minutes later with a finished record.
A local vinyl community
As a local musician himself, Schilling loves helping out bands on short notice. “We’ve worked with several artists where they call us and they’re like, ‘Hey, man, I have a show Friday night,’” he says. In such situations, he explains, American Vinyl Co. can quickly produce records that groups can then sell during their performances.
Meanwhile, Session at Citizen Vinyl also provides local artists with a place to promote their releases. “If artists want to have a record signing or release party, they can do that here,” Alder says.
The company’s building, previously owned by the Citizen Times, is itself a powerful reminder of the area’s music history: The third floor is the former home of WWNC, which broadcast radio pioneers such as Jimmie Rodgers and Bill Monroe & the Bluegrass Boys. Today, Citizen Vinyl’s founder Gar Ragland has restored the upstairs space where he runs his label, Citizen Studios.
“It’s just got a ton of that music history,” Sharp says of the space. And that, tied with Citizen Vinyl’s growing contributions to the building’s legacy, “really grabbed hold of me,” he adds.
Editor’s note: This story was updated on July 14.
Before you comment
The comments section is here to provide a platform for civil dialogue on the issues we face together as a local community. Xpress is committed to offering this platform for all voices, but when the tone of the discussion gets nasty or strays off topic, we believe many people choose not to participate. Xpress editors are determined to moderate comments to ensure a constructive interchange is maintained. All comments judged not to be in keeping with the spirit of civil discourse will be removed and repeat violators will be banned. See here for our terms of service. Thank you for being part of this effort to promote respectful discussion.