Burnsville resident Katherine Savage feels a unique kinship with a small patch of ground on the campus of Warren Wilson College. The 5-by-60-foot plot was home this year to a crop of flax, a traditional Southern Appalachian fiber plant, which she is helping process into linen that she will someday wear as her burial shroud.
Savage’s efforts to grow and fabricate the material in which she’ll eventually be buried may seem morbid in a society that abhors and fears death. But to the death midwife and self-described “death edu-culturist,” the process makes beautiful sense. Her work helps families and communities navigate — and normalize — death and dying through education, ritual, home funerals and sustainable body disposition using caskets or shrouds made from natural materials.
The early inspiration for the Field to Shroud project, says Savage, emerged from her experiences conducting home funerals in which families used treasured heirloom quilts for their loved ones’ shrouds. Indigenous author Martin Prechtel’s writings on Mayan culture and spirituality, as well as discussions Savage facilitated about shrouds during a death-focused women’s group, further nurtured the idea.
“I realized that my values had long been around keeping my circles strong and close to the earth, growing a lot of my own food,” she explains. “I knew then that I was going to be growing my own shroud.”
Cycle of growth
But the project was never intended as a solely personal journey. In fall 2019, Savage began seeking local collaborators who could help transform her idea into a community-focused effort. She imagined a multipronged mission of highlighting environmentally friendly burial practices, shifting cultural views about death and dying and fostering the development of a local flax-growing and linen-making industry.
That November, she connected with Warren Wilson College fiber arts instructor and Wild Earth Textiles owner Melanie Wilder. As an artist devoted to working with locally grown fibers and dyes, Wilder felt an immediate synergy with Savage’s vision. “I had always wanted to do a big gallery installation that talks about cloth from birth to death and the cycles in between and how we use cloth,” says Wilder. “So, I said, ‘Yes, let’s do this!’”
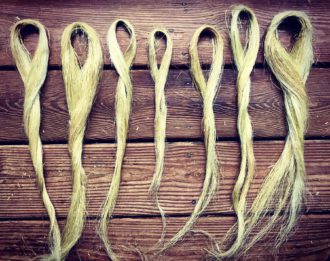
Wilder prefers using plant fibers over animal fibers, and because flax was historically grown and processed in Western North Carolina for individual and community use, it presented an obvious medium for the shroud. Savage sourced flax seeds specific to fiber production from the Netherlands, where flax growing is still widespread, and the two broadcast them by hand in mid-March (“when the first redbud leaves started coming out,” says Wilder) on a plot tilled for the project by the Warren Wilson garden crew.
From that point, Wilder says, the crop needed little attention. “It doesn’t really require any irrigation or amendments or weeding. It just kind of takes care of itself.” After about 100 days, when the plants were ready to be harvested, their small taproots allowed them to be pulled easily from the ground with roots intact.
Then came the real work of processing, accomplished with the help of Wilder’s fiber arts students. First, they soaked the plants in tanks of water for about four days, a process called retting that disintegrates the pectins in the woody stems.
Next, the partially decomposed plant material was air-dried before the more labor-intensive steps of braking, scutching and hackling. Those processes, respectively, break up the woody stems, scrape stem material from the fibers and comb out remaining impurities and short fibers. The resulting long, blond ponytails of flax strands are ready for spinning on wooden wheels into thread that’s woven into fabric on a loom.
Weaving community
Savage and Wilder initially planned to host community learning opportunities around each step of the project. “We envisioned many working circles happening in multiple realms engaging farmers and folks who work with healthy death practices and fiber artists or people who wanted to learn about the fiber process,” Wilder explains.
But COVID-19 forced them to scale back. Warren Wilson fiber arts students have helped some with spinning and weaving, and Savage and Wilder hosted two outdoor, socially distanced learning circles this fall at Wilder’s home in Swannanoa to process and spin the fiber. They also collaborated with local mutual aid initiative Cooperate WNC for an online webinar in late November focused on developing community-rooted death care practices.
“The hope was that we could begin to build some capacity in terms of other people wanting to try out some of these ideas or having some piece of the puzzle that they didn’t have to make it grow,” Savage says. “That momentum could then begin to lean toward becoming a mutual aid activity.”
Natasha Bowden, a farmer in Yancey County, has expressed interest in growing flax for the project, and Kathleen Wood of Dig In! Yancey Community Garden hopes to connect interested growers with relevant know-how. Savage and Wilder also plan to host a learning circle for area growers when it’s safe to hold large gatherings again.
The project’s long-term goals include building a dedicated WNC plant fiber processing facility. Flax, Wilder points out, can be processed on the same equipment as hemp, another fiber crop that’s rapidly gaining regional traction. “If we were able to scale up, we’d be able to process hemp as well, and I think that’s kind of the future of fibers,” she says, noting that small but successful flax and linen industries have successfully taken root in Northern California and Oregon.
A less tangible outcome for the project’s participants so far, says Wilder, has been a reconnection to the ancient tradition of sharing with one’s community the time-consuming, meditative work of processing fiber by hand. “People really seem to enjoy the process,” she says. “That has its worth, just as much as the monetary aspect of the whole economics around creating a local cloth infrastructure.”
One of the shroud’s three planned 2 1/2-by-10-foot fabric panels had been woven at press time, and work continues on the remainder. After washing and hemming, the undyed, finished shroud will measure 5 feet by 8 feet, and enough fiber from the harvest will remain for Wilder to create a sample shroud for future gatherings and classes.
“[The experience] has certainly been beautiful,” says Savage. “I think I’m just as excited about how it seems to be impacting people who are coming to these events and who hear the story of it as I am about the shroud itself.”
For more on Field to Shroud and Savage’s work as a death midwife, visit deathseedinglife.com.
I still treasure a kitchen towel made from flax grown by grandmother in Waynesville and also woven by her. Her name was Ruth Maney Williams; her home still stands in Waynesville.
I’m so glad for this project taking off now. God bless you! Virginia Nave Szenas