It’s easy to miss the turnoff on Sweeten Creek Road that leads to GE Aviation’s South Asheville operation. The service road winds through an industrial park, past several mundane structures and parking lots; employees move between GE’s two main buildings — the rotating-parts plant and the newer ceramic matrix composite facility.
But within those nondescript warehouse walls lies a world of robotics, high-tech devices and dynamic innovation, where a legion of highly skilled workers conceptualizes, develops and produces a dizzying array of flight components used by companies across the globe.
GE’s operation is just one example of how the local manufacturing sector is finding new life. With a bevy of companies relocating or expanding operations in Western North Carolina, economic boosters, educators and business representatives are working to prepare the next generation of workers to meet the growing need.
Ebb and flow
Since the arrival of the railroad in the late 19th century, manufacturing has played a vital role in the regional economy. For the next 100 years, the abundant raw materials and cheap, mostly nonunion labor encouraged manufacturers to produce a wide range of products here.
GE, for example, has been in the Asheville area since shortly after World War II, notes plant manager Michael Meguiar. “A lot of people are somewhat misinformed about that,” he says. “People mostly hear about our opening the new plant about two years ago; this site has actually been operating since the late ’40s.”
But while legacy companies like GE have stuck around, regional manufacturing gradually declined beginning in the 1980s. And between 2006 and 2010 alone, Buncombe County lost about 14 percent of its remaining manufacturing jobs, according to data provided by the Asheville Area Chamber of Commerce. During that same period, the Asheville Metropolitan Statistical Area (Buncombe, Haywood, Henderson and Madison counties) lost nearly 3,000 manufacturing positions.
Since then, however, Buncombe County has seen 16 percent growth in manufacturing jobs, and the Asheville metro added 1,982 of them, according to the Chamber of Commerce.
Wave of the future
This new wave, though, is “not your father’s manufacturing,” stresses Ben Teague, chief operating officer and executive director of the Economic Development Coalition. “It’s very sophisticated businesses that have great pay rates for career-type opportunities.”
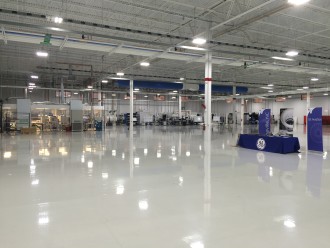
GE’s 2-year-old ceramic matrix composite facility is a shining example of the new face of manufacturing: The plant floor resembles a high-tech lab, with workers milling about in climate-controlled “clean” rooms, high-tech forges and tooling machines humming in neat rows, and robots ferrying parts from station to station, all under the watchful eye of technicians.
“When we first started this process, it was completely manual,” says aeronautical engineer Nolan Cousineau. But with growing production quotas on the horizon, Cousineau and his colleagues have worked to implement automated processes throughout the production line, streamlining tedious, repetitive tasks and freeing up employees to focus on more complicated functions.
“The technology is kind of a unique one where you’re having to handcraft something, but you’re taking the stuff that is ergonomically risky to the workforce and automating it,” Cousineau explains. “At first, our workforce was worried we were going to replace them with robots. But we’re not displacing people: We’re enabling them to do more.”
Spreading the word
Educating the public about the changing face of manufacturing, and getting young people interested in and trained for such careers, are keys to its continued local renaissance, says Nathan Ramsey, director of the Mountain Area Workforce Development Board. An arm of the Land of Sky Regional Council, the board works to create jobs in Buncombe, Madison, Henderson and Transylvania counties.
“Most people say, ‘Oh, those jobs have gone to China,’ but North Carolina is one of the largest manufacturing states in the country,” he points out. “It’s about 20 percent of our state’s economy.”
In the coming years, several manufacturing firms expect to expand their operations here, including GF Linamar (350 new jobs), BorgWarner Turbo Systems (154 jobs), Avadim Technologies (551) and others. Altogether, Ramsey predicts, 2,404 new positions will be added within the next 10 years through expansions and relocations.
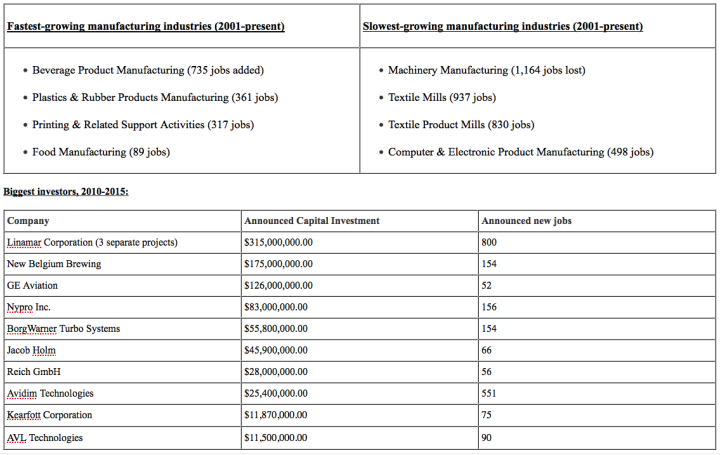
These companies manufacture a wide range of products. “Whether it’s plastic pipe, rocketry components or bottled juices — anything that you use on a daily basis — there’s probably a manufacturer in our region that had some part in making that,” he notes.
This new wave of manufacturing also offers lucrative career opportunities. In the second quarter of 2016, the manufacturing sector had the highest average weekly wage: $1,318, the Workforce Development Board reported in its December Regional Labor Market Snapshot.
Last year, the average weekly manufacturing wage in Buncombe County was $965.53, 26 percent above the county’s overall average weekly wage, according to the Asheville chamber. In the Asheville metro, the gap was 32 percent, with manufacturing jobs averaging about $976.22 weekly.
Perception problem
But if WNC’s manufacturing sector is experiencing a resurgence, it will be short-lived, says Ramsey, unless the region can provide a skilled workforce to support continued growth.
“Many parts of the workforce are aging; a lot of younger individuals are not as willing to consider a manufacturing career,” he notes. “If we can’t supply the talent, our local companies aren’t going to be able to grow and thrive here.”
And with so many job openings and the chance to learn transferable skills that pay a decent wage, why aren’t more young people pursuing those careers? Part of the reason is perception, says Jason Lorenz of Human Technologies Inc., a labor recruiting firm that works with manufacturers in the area.
“When I was growing up, manufacturing was kind of a bad word,” he explains. Many young people entering the workforce have been raised with the idea that obtaining a four-year degree is better than working in a factory.
Lorenz’s job, he says, is to re-educate students on what modern manufacturing is like. “If you look at a modern BMW plant, all the automation and how bright it is … there’s work cells right there on the floor where people are all on their laptops.” It’s a good fit, he says, for “kids who are into computer stuff.”
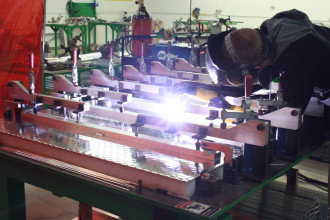
High-tech jobs
This new manufacturing reality, however, requires new skill sets, stresses Ramsey. “Even our entry-level manufacturing jobs, in many cases, require higher levels of skill than jobs did in the past. They’re high-skilled, really high-tech jobs. If they weren’t, they’d probably be someplace else.”
Acquiring those skills can be challenging, notes Rebecca Bruce, interim director of UNC Asheville’s joint engineering program. “It’s a very demanding curriculum that requires a very high credit-hour count to graduate,” she explains; not surprisingly, there’s a high attrition rate.
And while there are some local job opportunities for graduates, they’re still somewhat limited, says Maggie Hall, a senior in the program.
“I’ve looked at a couple of jobs in Asheville, but I’m probably going to move back to Raleigh, where I’m from,” she reveals. “In Asheville, there’s a handful of places that people in my program could end up working, but if I’m going to put down roots somewhere, I want to be reasonably confident that if, for whatever reason, I want to find another job, I can. In Asheville, those choices are fewer.”
Workplace learning
Efforts to recruit and support students interested in manufacturing careers extend from the classroom to the floor of the plants themselves.
“One of the systemic ways we’re working on that is the STEM school in Buncombe County,” Teague explains, referring to a curriculum that emphasizes science, technology, engineering and mathermatics. “Those kids are learning about the things that drive our economy.” And though it’s too soon to provide details, he continues, the Economic Development Coalition’s planned Campus Asheville initiative will be “a groundbreaking way of engaging students with the business community” to train and retain local talent.
Guiding students through the often lengthy processes leading to certification can make a world of difference, notes Lorenz. “You have to show this plan and say, ‘Hey, here’s what the whole path looks like: where you’d start, the commitment you’re going to have to make, the pay rate and the career path.’”
Partnerships between educational institutions and employers are also key. A-B Tech, for example, has classes in everything from machining fundamentals to aerospace and structural composites, and it’s considering launching an automation academy and other courses offering advanced workplace skills.
“New class offerings are generally based on industry request and need,” explains Debbie Cromwell, the school’s workplace learning coordinator. “We have increased our opportunity for students to participate in some form of workplace learning such as internships, special projects, pre-apprenticeships and apprenticeships.”
Revved up
UNCA’s joint engineering program, a partnership with N.C. State University, offers accreditation from both schools and training across a wide range of specialties, says David Erb, a lecturer in the program. “They’re getting a very broad-based engineering background,” he reports. “We’re keeping them very much generalists: The industry loves that.”

That broad scope of learning is part of what attracted Hall. “I felt like, with the way the world works now, it doesn’t make a lot of sense to divide up engineering disciplines the way it’s traditionally been done,” she says. “It would be much more beneficial to me and to my future employers to be able to know about all of the components.”
Thanks to UNCA’s small size and liberal arts orientation, students in the program get more face time with instructors, plus the chance to develop skills most engineering programs don’t emphasize. “Your typical engineering freshman lecture has 300 to 500 students in it; here, it’s 25,” notes Erb. “A liberal arts university is also different from a typical land-grant school in that it’s focused on that well-rounded-citizen approach. That’s really valuable to our students.”
Internships, career days and extracurricular projects like the Formula SAE challenge, in which students build an electric car from scratch, give them a chance to show employers that “they’re really revved up and are willing to go beyond just what classes require,” Erb maintains. “That tells those employers that these people care about the business.”
Teamwork
But the learning doesn’t end when students leave the classroom. Many manufacturers, including GE Aviation, are willing to train new employees on the job. “You don’t need to come in with composite experience; in fact, a majority of our workforce has no composite experience,” Cousineau says. “I actually like starting with blank slates, because you can teach them everything, and you don’t have to unteach bad habits.”
At the ceramic matrix composite facility, workers learn each part of the production process, from the initial cutting of materials to forging, machining and inspections. “To us, they’re all one technician,” says Cousineau. “If you don’t know anything, that’s OK: We’ll teach it all to you.”
Meanwhile, the facility’s team approach enables employees on the plant floor to self-direct daily activities. “The team is the one leading this — they control their own destiny here,” he explains. “They hold themselves accountable and negotiate who gets to work where.”
Allowing workers a say in daily operations gives the company a competitive edge, stresses Cousineau. “It builds that layer of ‘We can do this,’ versus ‘I’m being told to do this,’” he points out. “What that does is garner buy-in: They feel part of the victory and part of the solution.”
Commitment and camaraderie
For the team approach to work, though, employees must have a sense of shared responsibility and accountability. Often, says Lorenz, employers “are looking for three things: your attendance, your talent and your temperament. If you’ve got those, I can find a good home for you and expose you to that whole new different animal that’s growing in this area, even if you don’t have a background in manufacturing.”
At GE Aviation, notes Meguiar, “We very much run this plant like a family. Asheville and WNC are not only one of the greatest places in the country to live, work and play, but we have an awesome support system that respects and desires economic development and wants to grow manufacturing.”
Newer companies here share that sense of excitement. Since 2012, when Outdoor Gear Builders of WNC was formed, that industry has expanded by leaps and bounds, says Noah Wilson, the coalition’s director.
“We’ve seen a lot of growth and positive changes in outdoor products manufacturing in WNC. My inbox stays busy with inquiries from national brands looking to partner with our companies and awesome people reaching out about job opportunities with our members. This makes me confident that outdoor gear is only going to grow in impact as an economic driver.”
Being in a region known for its wide array of outdoor opportunities helps those businesses recruit a talented, engaged workforce, adds Wilson. “To build a great company, you need great people, and great people want to live in a great place. Asheville and WNC have grown tremendously in popularity in recent years, and that really helps with recruiting top talent. Equally important, we have an excellent manufacturing base.”
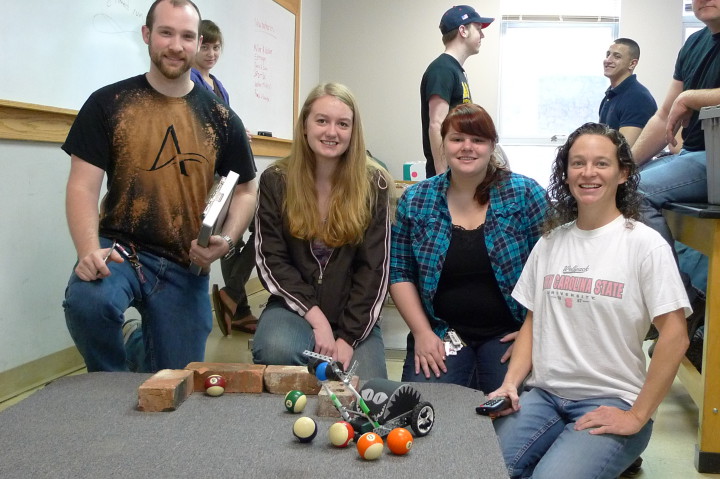
Rosie the Riveter redux
As educators and industry promoters alike look for new sources of labor to fill manufacturing positions, reaching out to women is a big focus, says Pamela Silvers, principal investigator for an A-B Tech pilot program aimed at improving training and increasing the number of jobs in technical fields. Women, she explains, constitute half the school’s student body but less than 15 percent of those enrolled in manufacturing-related programs.
“Manufacturing is often promoted because you can get well-paying jobs, which is how men often select their career,” says Silvers. “Women select careers because they want to help others, work in teams and make a difference. In order to major in a program, students must be able to picture themselves in a career, so we make sure we have females featured on promo materials,” she says.
Hall, meanwhile, says that of the roughly 30 students in her graduating class, only five are female. “We have a couple of great female faculty members that are very encouraging, but it’s definitely something that is always kind of present. I’ve had classes where I was the only girl. I don’t know if my male classmates notice it so much, but I can feel that I’m the only woman in the room.”
Despite their low numbers, though, “Women are always the curve-setters in engineering,” says UNCA’s Erb. “Women are here, generally, very intentionally: They have some reason to be here. That’s a categorically sexist statement, but it seems to hold true.”
Life-changing stories
Job expos and regional events like the Mountain State Fair, says Ramsey, also help recruit workers. Workforce Development Board representatives, he notes, recently traveled to Raleigh to accept WNC’s certification by the NCWorks Commission as an advanced manufacturing pathway in production, maintenance and engineering. The designation recognizes communities that, with support from the state, are striving to educate their residents about available career paths and provide training and resources to connect workers with companies.
The success of outreach efforts, Teague maintains, can be measured in the turnout for events like the Economic Development Coalition’s annual Homecoming Career Fair. “When I first got here in 2009, we had a total of 50 companies that would participate,” he recalls. Today, that number has more than doubled. “Last year, I think we had something like 4,000 job opportunities,” he continues. “I can tell you story after story of people who found their jobs there. It feels good to see lives change through that.”
Lorenz, too, has inspiring tales to tell. “The best story I have is about a kid who was working fast food, going to college; his girlfriend got pregnant right after high school. He told me, ‘I can’t keep doing this fast-food thing.’ I said, ‘I have an opportunity’ and showed him the plan.” Recently graduated, “He’s going from $9.50 to $15.45 an hour, which is life-changing for this guy. I’m pretty excited about that.”
Passing the torch
The next generation’s willingness to take advantage of such opportunities will be a key factor in sustaining the sector’s current boom, observers say.
“The demand for people who understand manufacturing will continue to rise,” Lorenz predicts, pointing to new product lines being launched at the BMW, Daimler and Volvo plants in South Carolina. “It’s really spreading out from Greenville-Spartanburg and making an impact here. The demand for advanced manufacturing is going to keep going up.”
And over at GE Aviation, Cousineau says he’s already seeing a changing of the guard. “A couple of years ago, I would have said we don’t have a lot of young talent,” he reveals. “But almost all the new hires, all the new engineers, are younger than me. It’s been a good thing, and we’ve been growing our talent pool.”
Meguiar agrees. “We feel very good about the future of manufacturing in Asheville,” he says. “If our local community continues to support growth in advanced manufacturing like they have with us, I think the future can be very bright.”
Below is a video outlining the work and projects conducted by N.C. State/UNC Asheville’s Mechatronics students during the fall 2016 semester. Video courtesy of UNC Asheville. To learn more, visit engineering.unca.edu/joint-bs-engineering-mechatronics-concentration.
I don’t think that manufacturing will ever grow in Buncombe county like they’d like it too. Logistically, it has a lot going against it. Land is expensive, and any direction you go transportation via tractor trailer is slow and hazardous due to the mountainous terrain and congested traffic.
Why would it LOL? The area is nothing more than a glorified puke bag. Look an hour a way and the names that are located there. BMW, Michelin, Lockheed Martin, GE Turbine, etc. Further down towards the coast is Boeing. They want to bring jobs to South Carolina. They don’t want jobs here that actually put the working class on equal footing with the pseudo-intellectual credentialed class. A strong working class here is a threat to them. Their tourist traps and overpriced slop shops wouldn’t be the end all to be all. Their stranglehold on the government would be loosened. What working class person wants to pay more taxes for the RAD, greenways that they’ll never use, and subsidize millionaire hotel owners? It’s why the loons here pay lip service while not ever caring to empathize or even understand just how bad their policies really are to the working stiffs. And why they write articles now about the housing crisis easing, notice that rents and costs are not and never will go down? How can they when gentrification is in full force via higher and higher taxes, fees, and cost.
I’ll expand on the working class by saying the establishment wants a workforce that’s dependent on their rules and regulations. Not a highly payed working class that votes conservative and doesn’t vote in people who will waste their money. But as many are aware, those in government positions are some of the most stupid people around. They are clueless when it comes to jobs. Unless of course they are looking to keep theirs or those of their crony friends.
Haters gonna hate, hate hate. Conspiracy loons gonna loon.
Are you running for office, then? Put up or shut up.
“Land is expensive, and any direction you go transportation via tractor trailer is slow and hazardous”
Huh? What do you think “manufacturing” means? Linamar makes engine parts; AvL Technologies makes mobile antennas. All those breweries are manufacturing beer. We have interstate highways, freight rail and an airport. If the only thing that comes into your head for “manufacturing” is a car plant or tire plant on 20 acres like the ones in GSP, then your head is a very cramped space.
Not a lot of growth in the past 25 years is it? And yeah, I tend to think of growth in terms of plants that employ several hundreds, rather than several dozens.
Sounds like Snowflake is our new go to guy for local economics.
Snowflake, do you currently like near Asheville?
I’ve seen you dodge that question on another thread.
Yep, I do live here.
He’s a master in both comparative religion and economics, as long as the ideas are pulled from his you know where.
“I tend to think of growth in terms of plants that employ several hundreds, rather than several dozens.”
That’s one way to think about it… if you’re stuck in the 1950s. In the meantime, there are lots of small-scale German companies that prosper on making one thing well, especially “the vital parts for the machines that make the things”, and that’s the kind of industry that can grow in WNC. Not going to get Beacon Mill back.
German companies- now your’e a speaking Snowflake’s language, circa 1938.
I encourage you and other posters to continue asking if he lives here for being the Karl Korrect Kommentator .
It made me really happy a while back to discover Peck lives in Texas, yet still can’t stand how a little ol city works from about 10 hours awy by Kar.
No, I do not live in Asheville. I live in the area. If I have my druthers, I will never live inside the city limits again.
“In the meantime, there are lots of small-scale German companies that prosper on making one thing well, especially “the vital parts for the machines that make the things”, and that’s the kind of industry that can grow in WNC. ”
That’s true, but that growth hasn’t happened in the area to a large degree either. And the reason I have a preference for big companies is because that’s where the money is. And they really are what drives most of these smaller businesses you mentioned.
Live, not like. I sometimes don’t feel the spirit of proofing for responding to one trick ponies.
Giddyup.