Surprise marks most customers who first enter The Watchmaker’s Shop inside the Grove Arcade. Even after they’ve Googled where to take their broken timepiece, their disbelief is apparent. “They literally come in and say, ‘I didn’t even know you guys still existed,’” says watchmaker Sergio Berrios.
For Berrios, this shock is indicative of the times. “We’re very much living in a disposable society,” he says. “You can pretty much order anything on Amazon, get it here in two days, and if it lasts a certain amount of time, you’re not [upset] that it broke.”
In contrast to the throwaway culture, The Watchmaker’s Shop is one of several esoteric repair shops scattered throughout Asheville and Western North Carolina. Some fix saddles, while others service slot machines. Shoes, shirts and cameras are also on the table.
For Amber Weaver, sustainability officer for the city of Asheville, such businesses play a crucial role in the city’s goal of sustainable consumption; these operations mean reusable items are staying out of the landfill. But the mere existence of these shops doesn’t suggest the issue of excess waste is resolved. “Research and practices continue to change as technology improves, and it’s important to educate the citizens of Asheville on what’s offered,” says Weaver.
Technology aside, in some cases it’s as simple as realizing that repair options are available. Weaver points out a pair of boots she’s owned for the past 23 years. “I recently had them resoled at Jackson’s,” she says. “I’ll never let [them] go.”
A family trade
Jackson Trading Co. was opened in 1938 by local businessman Stonewall Jackson. It began as a men’s clothing store on Lexington Avenue. But after World War II, Stonewall’s sons, Julian and Thomas, expanded the business. Among its new offerings was leather repair. By the early 1970s, the shop relocated to West Asheville, where it was eventually rebranded Jackson’s Western Store. Cousins John and Charles Jackson continue to operate the family business.
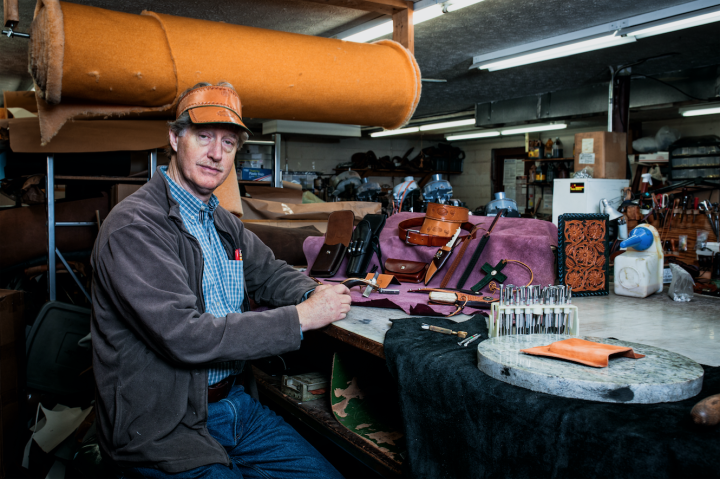
The store still offers leather repair in a three-man shop set up in the building’s basement. Rick Sluder and Larry Wade manage most of the damaged cowhide, with additional help from John Jackson. On average, they see 20-25 saddles per month. Along with horse gear, the shop mends items such as baseball gloves, ammunition belts and pocketbooks.
Century-old tools, including rivet machines, harness stitchers and a handmade instrument called the deadman (used for stripping hides), are stationed throughout the space. Near the back end, stacks and rolls of leather line the wall. The hides are used for repair, as well as custom-made cellphone cases, belts and gun holsters. “Nobody took courses,” John Jackson explains. “We learned it on the go. That’s probably why there’s so many pieces of scrap leather [lying around].”
While repairs keep the team busy, John Jackson concedes that the majority of business takes place upstairs on the retail end. Nostalgia, he believes, is what leads patrons down the stairs; the shop allows visitors to step back in time to see a practice that dates back centuries.
Put another dime in the jukebox, baby
Nostalgia also plays a factor in Don Frederick’s business, For Your Amusement. Based in Black Mountain, the one-man shop offers over 30 years’ experience in repairing all coin-operated machines.
Of late, pinball machines have made up the majority of Frederick’s business. But a handful of jukeboxes hang out in the shop, as well. Among them is a 55 Seabird — Frederick’s next big project. The jukebox belonged to a client’s recently departed mother, Frederick says. “It’s got sentimental value,” he explains. “A lot of [my business] is like that.”
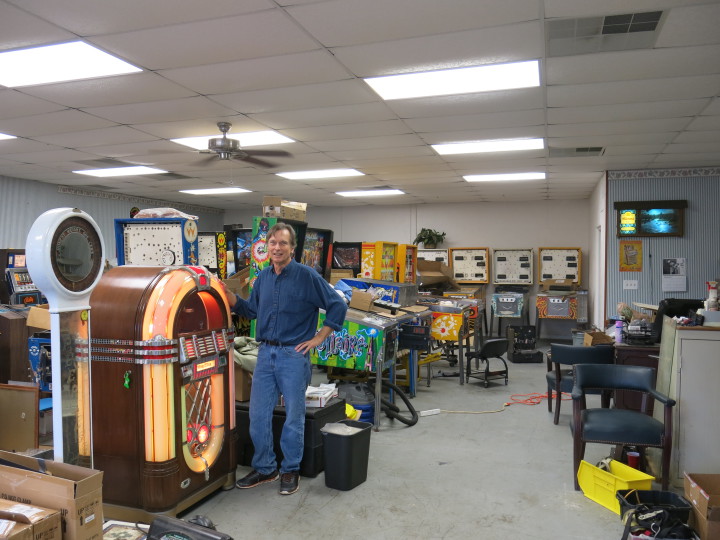
On any given week Frederick clocks in 40-60 hours. While the majority of his business is based in Asheville, he’s made house calls to Charlotte, Winston-Salem, Greensboro and Raleigh. It’s not uncommon for clients to drive in from neighboring states to deliver machines in need of repair. (In fact, while Frederick showed Xpress around his workspace, a client from Knoxville, Tenn., came in with his son’s slot machine.)
The holidays are Frederick’s busiest time of year. As families reunite and dust the cobwebs off the old arcade games and pinball machines, they discover the previous 11 months of relative inactivity have rendered the equipment useless. Frederick compares it to a car left sitting in the driveway. “You’re going to have problems,” he says. “The people who play their games the most have the least amount of issues. … Even if you’re just shooting the ball and walking away.”
Despite steady business, Frederick says many customers assume the work is a side gig. “They’ll ask, ‘What do you do for your real job?’” he says. “I’m like, ‘This is what I do; I make a living doing this.’”
A mile in his shoes
Not all repairs come out of a place of tenderness — some are to save the tenderfooted. Inside Tong Kim’s River Ridge Shoe Repair, sneakers, boots, sandals and cleats surround the cobbler, while shoe polish and glue permeate the air.
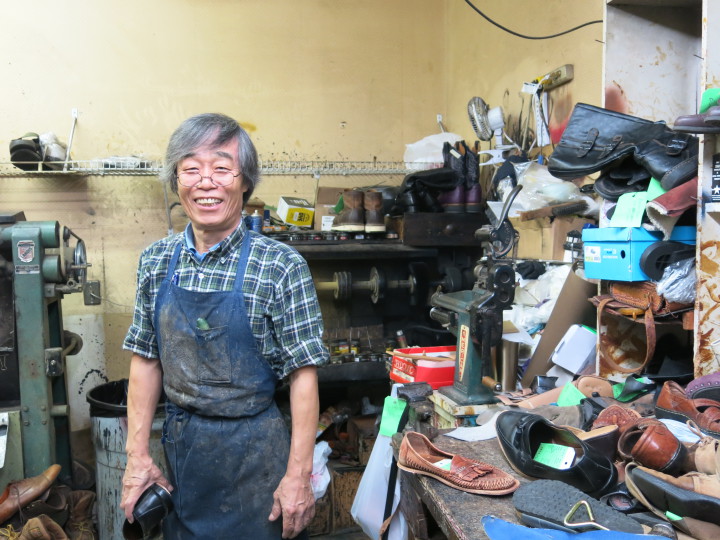
Kim says on an average day, he’ll mend anywhere from 50 to 70 shoes. The demand is evident; he doesn’t stop working as he discusses his 46 years in the business. Boot after boot gets resoled, then tossed to the side, as he brings up his early years in Korea, where he began as a shoemaker. By the time he arrived in Asheville in the 1970s, he applied his skill set to a different side of the trade. “When I came here, nobody wanted to pay that kind of money” for designer shoes, he says. “So I had to start repairing shoes so I could eat.”
The quality of shoes being produced has declined over the past four decades, Kim maintains. “It’s not as good as it used to be,” he says. “Rubber, leather — I think [the manufacturers] are trying to cut corners.” Of course, this translates to steady business for the shoe repairman.
Among the mountains of footwear, Kim points out other items on the shelves. Leather jackets, bags and suitcases are scattered throughout the shop. “Anything leather, I’ll repair,” he says as he resoles another boot.
Turn, turn, turn
Like River Ridge Shoe Repair, there is no shortage of work at Misha’s Alterations and Tailor. Owner Misha Davidshuk opened the shop in 2002, after he and his family relocated to Asheville from Belarus. Since that time, the family business, located at 5 Regent Park, has grown. His daughter, Tatyana, recently joined her father after completing her entrepreneurship certificate at A-B Tech.
Tatyana Davidshuk says when it comes to alterations, clothing isn’t the only thing with patterns. “We’re getting into the winter coat season,” she explains. Come spring, prom dresses will line the racks. Once summer hits, wedding dresses reign supreme.
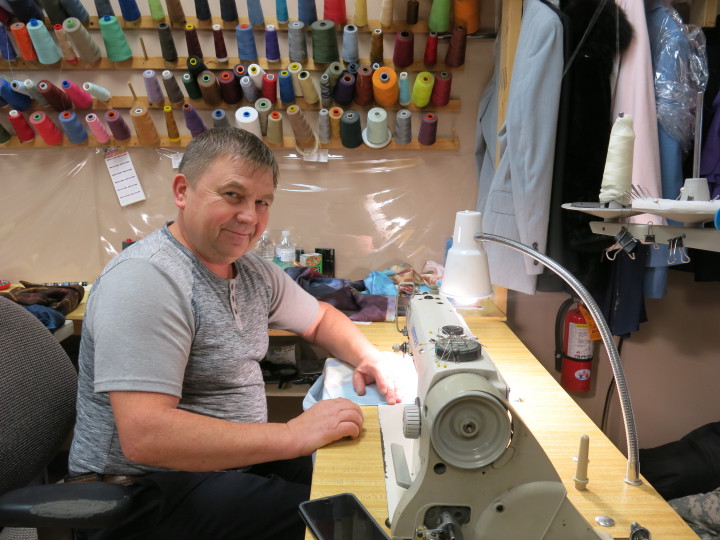
While clothing makes up the majority of the shop’s work, the business has seen a few unique projects in its day. In one instance, Tatyana Davidshuk says, a customer brought in a bearskin. It was her father’s job to turn that bearskin into a proper rug.
Like many of the proprietors of specialty repair shops who spoke with Xpress, word-of-mouth has been the lifeline for the steady stream of work at Misha’s Alterations and Tailor. “We’re not very good on social media,” Tatyana Davidshuk concedes. But that hasn’t slowed them down. She estimates that the shop’s annual numbers of mending jobs are in the thousands, noting that they mend at least 100 pairs of pants each month.
And while some of the business comes from neighboring states, as well as one loyal customer based in California, most of their time, energy and stitchings are spent on local clients’ wares. “We’re not trying to reach above and beyond what we can actually take on,” Tatyana Davidshuk explains.
In focus
In order for word-of-mouth to spread, folks need to be talking. In 1982, George and Debra Hall opened Crystal Camera Repair in West Asheville. In the early days, Debra Hall says, the husband-and-wife team would literally knock on doors in order to tell people about the services they provided. Now, after more than 35 years in business, she says the shop has repaired more than 99,000 cameras.
From 16 millimeters to helmet cams, the business has adapted to the ever-changing industry. In addition to serving both professional photographers and hobbyists, the repair shop also handles accounts for larger institutions such as hospitals, churches and universities.
Just as the technology has changed, so too has the inner working of the industry itself. Certain manufacturers, says Debra Hall, now have restrictions on parts. That means in some cases, Crystal Camera Repair is unable to work on a particular brand. Instead, customers are required to mail their camera to the manufacturer. Not surprisingly, this is a more expensive and time-consuming endeavor. (A similar issue is at play within the watch industry.)
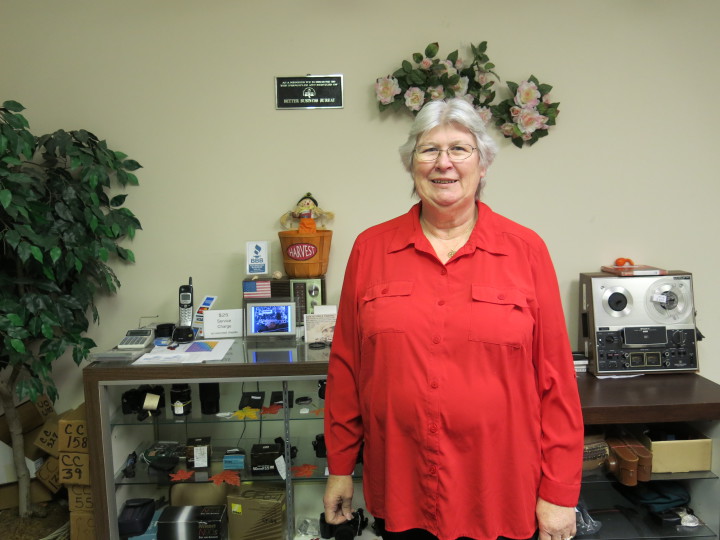
Nevertheless, the company’s reputation has continued to grow, stretching beyond the mountains of WNC. In its main lobby, a map of the U.S. is marked with red dots highlighting areas it has served. Nebraska, North Dakota, Wyoming and Nevada appear to be the business’s only remaining holdouts within the continental U.S. Meanwhile, Crystal Camera Repair has also shipped parts around the world, including England, Ireland and Scotland. In one instance, Debra Hall says, they mailed a package to a weather station in Antarctica.
Many customers also bring cameras in from far and remote places. “We’ve noticed a lot of people tour Africa,” Debra Hall says. “You can almost tell what area they were in because the African dust is different [from region to region]. In some areas it’s white, like talcum powder. In others it has a reddish tint. And in some [locations] it’s more a brownish gray.”
When it comes to caring for a camera, Debra Hall has plenty of advice. First, she says, avoid moisture. Fungus can and will grow on cameras (especially on cameras left in damp cases). Second, keep it clean. Dust and other debris won’t only ruin a shot, but could also damage the camera. Third, mind your camera’s battery. Corrosion can lead to an expensive repair job; if you don’t plan to use your camera for an extended period, take the battery out.
Keep it aboveground
In 2014, Asheville City Council passed a resolution calling on the city to reduce its landfilled waste by 50 percent come 2035. According to Jessica Foster, the city’s solid waste manager, progress is being made. Despite a rise in population, Foster says, “we have reduced landfilled waste by almost 7 percent, which has resulted in an additional $77,000 in savings in landfill disposal fees.”
Despite these promising numbers, Foster says the city has a long way to go. “For the past few years, we do seem to be hovering around the 22,000 tonnage mark,” she says. “It will require increased waste reduction efforts to meet our 50 percent reduction goal.”
Reuse is one of the key components for the resolution’s success. Foster says a 2015 audit found that landfill waste consisted of 18 percent recyclable goods. She believes educational programs, as well as services such as repair shops, “will help us move closer to our goal.”
Meanwhile, back at The Watchmaker’s Shop, Berrios’ steady stream of repair jobs suggests certain items are irreplaceable. “People still want to fix their dad’s watch that got handed down to them,” he says. “It doesn’t just get chucked in a drawer and [replaced by] a new one.”
Great piece. I’m a satisfied customer of three of the businesses featured, and will probably be using a fourth soon. The only way those skills stick around is by supporting them, and by having young people willing to learn the skills as apprentices in the knowledge that it’s a worthwhile investment of their time and energy.